
VLM enables formulations with more modifiers and ingredients because it can process resins that are 50 times more viscous than the industry standard, which then opens up new mechanical and thermal properties. The production-oriented process uses high viscosity resins to print high-performance parts for less money, at a higher speed. The next Dyndrite announcement is that the first generation of BCN3D‘s patented Viscous Lithography Manufacturing (VLM) technology will be powered by its software.
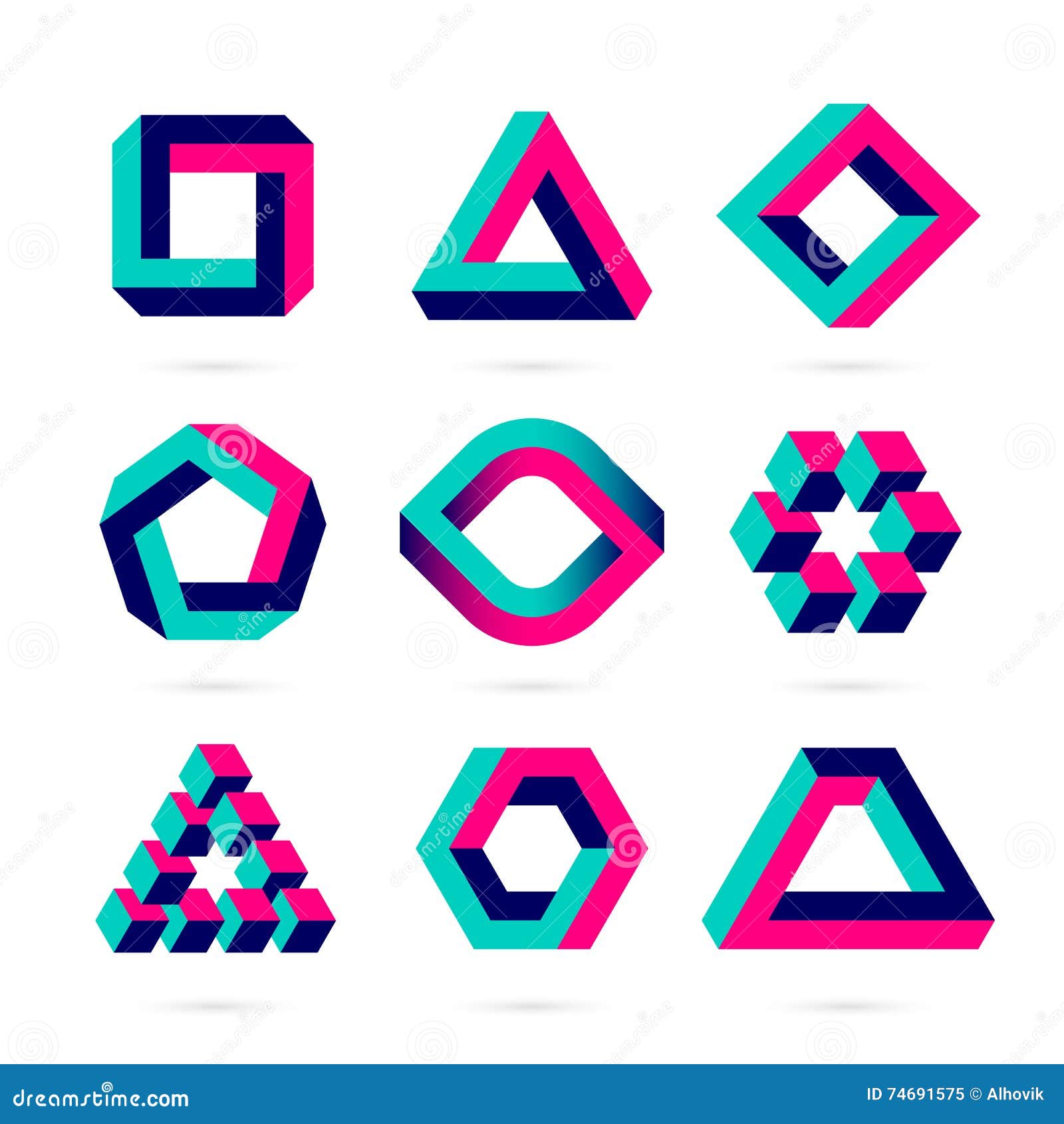
#3d impossible shapes software#
The app development process has been simplified, and allows Impossible Objects to iterate on their software quickly. The ON-RAMP app was built and branded using the Dyndrite ADK.
#3d impossible shapes manual#
The Dyndrite-driven solution also achieves a 90% reduction in manual labor, 20% improved build block use, faster processing of native CAD 3D data, customizable workflows, and more. The software offers a programmable, automated CAD-to-print workflow with a much faster build time and traceable, repeatable parts, as well as an easy-to-use GUI. The proprietary Rules-based Automated Masking Packing and Slicing (ON-RAMP) software by Impossible Objects is powered by Dyndrite, and drives the CBAM process by integrating Dyndrite’s GPU-accelerated, Python-based ACE. “This achievement is not only a great feat for Impossible Objects, but for our industry – it moves 3D printing into a new category of volume manufacturing.”ĬBAM 25 is durable and simple to maintain, operates at room temperature, and is easy to operate, and the machines will be available early next year. For a speed comparison, this is the difference between the fastest human and a Formula 1 car in covering a mile,” said Robert Swartz, Founder and Chairman of the Board at Impossible Objects. Our new CBAM 25 process now operates fifteen times faster than the nearest competitor, while delivering the superior material properties required for industrial-grade end-use parts.

“Impossible Objects pioneered the CBAM process, bringing an unprecedented level of part durability to additive manufacturing. CBAM 25, which uses roll-fed inkjet technology, is said to be 15 times faster than its competitor processes, with a continuous printing rate of 25 feet per minute, or almost 11,000 cm^3/hr of parts printed per hour. Impossible Objectsįirst, Impossible Objects is using Dyndrite’s ADK to power its high-speed composite-based additive manufacturing process.

Dyndrite’s LPBF materials and process software can help control surface roughness, tailor print parameters for complex geometry, enable methods for developing angle-based print support requirements, and more.Īdditionally, Dyndrite made several announcements before and during the event. The Seattle-based AM software company, which developed its Accelerated Computation Engine (ACE) and Application Development Kit (ADK) to help customers create digital manufacturing software and hardware, showcased a group of parametrically-created Laser Powder Bed Fusion (LPBF) builds representing several metal 3D printer providers, including Aconit圓D, EOS, Renishaw, and SLM Solutions, for which it provides native file integration. Now, lotus will prove again to the world the edge that 3D-printing will offer to the construction industry when it comes to free-form structures," Gandhi added.Like so many other 3D printing companies, Dyndrite attended the recent RAPID + TCT, North America’s premier annual additive manufacturing trade show. "But we have already proved with our Ganesha temple that shapes that are almost impossible to attain with conventional techniques can be done easily using 3D technology. "We are hoping that what we learned from the 'modak' will let us finish the 'lotus' earlier than that," said Gandhi. With the Shivalay and the modak completed, phase II comprising the Lotus and the tall spires (gopurams) are underway," Jeedipalli added.ĭespite being a challenge, the dome-shaped modak, which required the team to get innovative, took the team only about six hours to print it over a span of 10 days, Gandhi said. The team is now working on the lotus shaped temple dedicated to Goddess Parvati. After undergoing load testing and evaluation for functional use, it is now being used as pedestrian bridge in the garden around the temple," said Dhruv Gandhi, CEO of Simpliforge Creations.

The concept and design were developed and evaluated by Prof K V L Subramaniam and his research group from the civil engineering department of IIT Hyderabad. "This was also assembled on site at Charvitha Meadows, Siddipet.
